ALDEHIDOS, CETONAS, ÁCIDOS CARBOXÍLICOS Y DERIVADOS EN LA INDUSTRIA, EN LA VIDA COTIDIANA Y LA SALUD
1. Propiedades, preparación y usos de los aldehídos y las cetonas (fabricación de resinas y plásticos)
De todos los compuestos orgánicos, los aldehídos y las cetonas son los que más se encuentran, tanto en la naturaleza como en la industria química. En la naturaleza, una buena parte de las sustancias necesarias para los organismos vivos son los aldehídos o cetonas. En la industria química se producen aldehídos y cetonas simples en grandes cantidades para utilizarlas como disolventes y materias primas, con el fin de preparar muchos otros compuestos.
En la Química Orgánica existen agrupaciones de átomos que les confieren a los compuestos orgánicos sus características químicas, o capacidad de reaccionar con otras sustancias específicas. Son los llamados Grupos Funcionales. La mayor parte de las sustancias Orgánicas solo se componen de Carbono, Oxígeno e Hidrógeno, pero la forma en que están enlazado estos elementos puede dar origen a distintos compuestos, que pertenecerán a distintos Grupos funcionales, como lo son los aldehídos y las cetonas.
Definición de Cetonas y Aldehídos
Los aldehídos y las cetonas son funciones en segundo grado de oxidación. Se consideran derivados de un hidrocarburo por sustitución de dos átomos de hidrógeno en un mismo carbono por uno de oxígeno, dando lugar a un grupo oxo (=O). Si la sustitución tiene lugar en un carbono primario, el compuesto resultante es un aldehído, y se nombra con la terminación -al. Si la sustitución tiene lugar en un carbono secundario, se trata de una cetona, y se nombra con el sufijo -ona.
El grupo funcional conocido como grupo carbonilo, un átomo de carbono unido a un átomo de oxigeno por un doble enlace- se encuentra en compuestos llamados aldehídos y cetonas.
En los aldehídos. El grupo carbonilo se une a un átomo de hidrógeno y a un radical Alquilo, con excepción del formaldehído o metanol.
En las cetonas, el carbonilo está unido a dos radicales que pueden ser iguales, diferentes, alquílicos. La fórmula abreviada de una cetona es RCOR.
Los aldehídos y las cetonas son muy reactivos, pero los primeros suelen ser los más reactivos.
El grupo carbonilo se encuentra unido a dos radicales hidrocarbonados: si éstos son iguales, las cetonas se llaman simétricas, mientras que si son distintos se llaman asimétricas.
Según el tipo de radical hidrocarbonado unido al grupo funcional, Los aldehídos pueden ser: alifáticos, R-CHO, y aromáticos, Ar-CHO; mientras que las cetonas se clasifican en: alifáticas, R-CO-R', aromáticas, Ar-CO-Ar, y mixtas; R-CO-Ar, según que los dos radicales unidos al grupo carbonilo sean alifáticos, aromáticos o uno de cada clase, respectivamente.
Nomenclatura de Aldehídos y Cetonas
Para denominar los aldehídos y cetonas se puede usar el sistema IUPAC. En ambos casos primero se debe encontrar la cadena hidrocarbonada más larga que contenga al grupo carbonilo. La terminación -o de los hidrocarburos se reemplaza por -al para indicar un aldehído.
Las cetonas se denominan cambiando la terminación -o de la cadena carbonada lineal más larga que contienen al grupo carbonilo por la terminación -ona del carbonilo en la cadena carbonada.
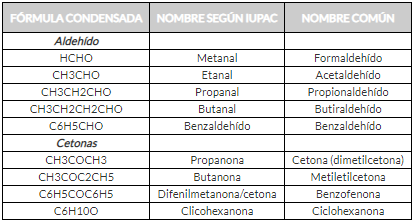
Las características especiales del grupo carbonilo influyen en las propiedades físicas de las cetonas y de los aldehídos.
Punto de ebullición: temperatura de ebullición mayor que hidrocarburos del mismo peso molecular, pero menor que el de los alcoholes y ácidos carboxílicos comparables. Esto se debe a la formación de dipolos y a la ausencia de formación de puentes de hidrógeno intramoleculares en éstos compuestos.
Los aldehídos y las cetonas no pueden formar enlaces intermoleculares de hidrógeno, porque al carecer de grupos hidroxilo (-OH) sus puntos de ebullición son más bajos que los alcoholes correspondientes. Sin embargo, los aldehídos y las cetonas pueden atraerse entre sí mediante las interacciones polar-polar de sus grupos carbonilo y sus puntos de ebullición son más altos que los de los alcanos correspondientes.
Con excepción del metanol, que es gaseoso a la temperatura ambiente, la mayor parte de los aldehídos y cetonas son líquidos y los términos superiores son sólidos. Los primeros términos de la serie de los aldehídos alifáticos tienen olor fuerte e irritante, pero los demás aldehídos y casi todas las cetonas presentan olor agradable por lo que se utilizan en perfumería y como agentes aromatizantes.
Solubilidad: a medida que aumenta el tamaño de las moléculas, disminuye la solubilidad de los compuestos. Los aldehídos y las cetonas pueden formar enlaces de hidrógeno con las moléculas polares del agua. Los primeros miembros de la serie (formaldehído, acetaldehído y acetona) son solubles en agua en todas las proporciones. A medida que aumenta la longitud de la cadena del hidrocarburo, la solubilidad en agua decrece. Cuando la cadena carbonada es superior a cinco o seis carbonos, la solubilidad de los aldehídos y de las cetonas es muy baja. Como era de suponer, todos los aldehídos y cetonas son solubles en solventes no polares.
Estado físico: bajo peso molecular (gases), peso molecular intermedio (líquidos) y compuesto pesados (sólidos).
Propiedades químicas
Las cetonas y los aldehídos se comportan como ácidos debido a la presencia del grupo carbonilo, esto hace que presenten reacciones típicas de adición nucleofílica.
- Reacciones de adición nucleofílica
- Reducción o hidrogenación catalítica
- Reacciones de sustitución halogenada
- Reacciones de condensación aldólica
- Reacciones de oxidación.
Aplicaciones de Aldehídos y Cetonas
Se ha aislado una gran variedad de aldehídos y cetonas a partir de plantas y animales; muchos de ellos, en particular los de peso molecular elevado, tienen olores fragantes o penetrantes. Por lo general, se les conoce por sus nombres comunes, que indican su fuente de origen o cierta propiedad característica. A veces los aldehídos aromáticos sirven como agentes saborizantes. El benzaldehído (también llamado "aceite de almendra amargas") es un componente de la almendra; es un líquido incoloro con agradable olor a almendra. El cinamaldehído da el olor característico a la esencia de canela. La vainilla que produce el popular sabor a
vainilla durante un tiempo se obtuvo solo a partir de las cápsulas con formas de vainas de ciertas orquídeas trepadoras. Hoy día, la mayor parte de la vainilla se produce sintéticamente:
La vainillina es una molécula interesante porque tiene diferentes grupos funcionales: unos grupos aldehídos y un anillo aromático, por lo que es un aldehído aromático.
El alcanfor es una cetona que se encuentra en forma natural y se obtiene de la corteza del árbol del mismo nombre.
Tiene un olor fragante y penetrante; conocido desde hace mucho tiempo por sus propiedades medicinales, es un analgésico muy usado en linimentos. Otras dos cetonas naturales, beta-ionona y muscona, se utilizan en perfumería. La beta ionona es la esencia de violetas. La muscona, obtenida de las de las glándulas odoríferas del venado almizclero macho, posee una estructura de anillo con 15 carbonos.
El aldehído más simple, el formaldehído, es un gas incoloro de olor irritante. Desde el punto de vista industrial es muy importante, pero difícil de manipular en estado gaseoso; suele hallarse como una solución acuosa al 40 % llamada formalina; o en forma de un polímero sólido de color blanco denominado paraformaldehído.
Si se caliente suavemente, el paraformaldehido se descompone y libera formaldehído:
La formalina se usa para conservar especímenes biológicos. El formaldehído en solución se combina con la proteína de los tejidos y los endurece, haciéndolos insolubles en agua. Esto evita la descomposición del espécimen. La formalina también se puede utilizar como antiséptico de uso general. El empleo más importante del formaldehído es en la fabricación de resinas sintéticas. Cuando se polimeriza con fenol, se forma una resina de fenol formaldehído, conocida como baquelita. La baquelita es un excelente aislante eléctrico; durante algún tiempo se utilizó para fabricar bolas de billar.
El acetaldehído es un líquido volátil e incoloro, de olor irritante. Es una materia prima muy versátil que se utiliza en la fabricación de muchos compuestos.
Si el acetaldehído se calienta con un catalizador ácido, se polimeriza para dar un líquido llamado paraldehído.
El paraldehído se utilizó como sedante e hipnótico; su uso decayó debido a su olor desagradable y al descubrimiento de sustitutos más eficaces.
La cetona industrial más importante es la acetona, un líquido incoloro y volátil que hierve a 56° C. Se utiliza como solvente de resinas, plásticos y barnices; además es miscible con agua en todas las proporciones. La acetona se produce en el cuerpo humano como un subproducto del metabolismo de las grasas; su concentración normal es menor que 1 mg./100 ml de sangre. Sin embargo, en la diabetes mellitus, la acetona se produce en cantidades mayores, provocando un aumento drástico de sus niveles en el cuerpo.
Aparece en la orina y en casos graves se puede incluso detectar en el aliento.
La metilcetona se usa industrialmente para eliminar las ceras de los aceites lubricantes, durante la refinación; también es un solvente común en los quita esmaltes de las uñas.
Resinas de policondensación: Obtención de Nylon
INTRODUCCIÓN:
La primera fibra totalmente sintética producida fue el Nylon, en 1935. Es un polímero constituido por moléculas de largas cadenas, de elevada masa molecular y longitud variable.
PROPIEDADES:
El nylon tiene una gran resistencia a la rotura, gran elasticidad y baja densidad. Funde a temperaturas del orden de 260 ºC y se reblandece a la temperatura de 180ºC. Se obtiene por polimerización de condensación una pasta filamentosa y blanquecina, que al enfriar se vuelve elástica y resistente. Arde suavemente y se funde. Es bastante estable frente a agentes químicos.
APLICACIONES:
Al principio el nylon no era más que una curiosidad de laboratorio, su primera aplicación fue la fabricación de medias en sustitución de la seda natural (1940) y para la fabricación de paracaídas utilizados en la 2ª Guerra Mundial. El carácter hidrófobo de estas fibras las hace adecuadas para su empleo en la fabricación de impermeables, bañadores, etc, prendas que hasta su invención no se conocían con estas propiedades.
PROCEDIMIENTO. OBTENCIÓN DEL NYLON:
1. Preparar una disolución de 0.4 ml. de cloruro de adipoilo en 20 ml. de tetracloruro de carbono. (disolución A).
2. Preparar una disolución de 2,2 g de hexametilendiamina y 1.5 g de hidróxido de sodio en 50 ml. de agua. (disolución B)
3. Añadir 16 ml de la disolución A a un vaso de precipitados y 20 ml de la disolución B a otro vaso.
4. Lentamente y con cuidado añadir la disolución B en el vaso de la disolución A. Observe que se forman dos fases, el nylon se forma en la interfase de las dos superficies, que retiraremos estirando y enrollándolo en una varilla de vidrio.
5. Lavar el nylon con agua y dejar secar.
FUNDAMENTO QUÍMICO:
MONÓMEROS: Cloruro de decadioilo y 1,6-diaminohexano.
Cada vez que se unen dos monómeros se elimina una molécula de cloruro de hidrógeno, y los extremos de la molécula formada pueden volver a reaccionar para formar moléculas muy largas, formando el nylon 610:
Cl-CO-CH2-C H2-C H2-CH2-C H2 C H2 C H2-C H2-CO-Cl+ H-NH-(CH)6 -NH-H
Cl-CH2-CH2-CH2-C H2-C H2-CH2-CH2-C H2C H2-C H2-N-C H2-CH2-CH2-CH2-C H2-C H2-NH2 + HCl
Moldeo por contacto a mano
INTRODUCCIÓN
El moldeo por colocación manual o moldeo por contacto, denominado así debido a las bajas o nulas presiones que necesita el procedimietno, fué la primera técnica que se empleó en el laminado de los plásticos reforzados con fibra de vidrio y hoy es todavía uno de los procesos más utilizados.
En producciones de series indsutriales cortas y piezas de gran superficie es el método más económico al presentar las ventajas de su relativa sencillez y no requerir mano de obra excesivamente especializada ni inversiones extraordinarias.
Por el contrario, prsenta los inconvenientes de un ambiente de trabajo molesto, prodccuón lenta, mayor necesidad de mano de obra, acabado fino sólo por la ara de la pieza en contacto con el molde y calidad final sometida a la especialización y sensibilidad del operario.
Indudablemente, las características mecánicas y físicas alcanzadas mediante el estratificado a mano son inferiores a las obtenidas por cualquier otro método de transforamción (moldeo de presna, por ejemplo), debido sobre todo a la limitación que tiene este procedimiento en cuanto al porcentaje de fibra de vidrio de las piezas moldeadas, qeu se sitúa entre el 25 y 40% al utilizar el mat y el 40 y 60% utilizando tejido. No obstante, una cuidada selección del refuerzo y una oportuna colocación del mismo conducen la obtención de partes estructurales eficientísimas, tal y como se demuestra en la enorme diverisdad de aplicaciones en multitud de campos.
Cualquier pieza que exija unas determinadas pretaciones, será elaborada de una forma diferente en cuanto al tipo y númeo de capas de refuerzo, pero el método de fabricación será siemrpe idéntico cuando apliquemos el procedimietno que se especifica a continuación.
FUNDAMENTO
El moldeo por contacto a mano se vasa en la combinación de un material líquido, que habitualmente es una resina de poliéster, y un material sólido, fibra de vidrio, en diferentes prestaciones.
Por medio de un sistema catalítica, se provoca la reacción química que conduce al endurecimietno controlado de laresina.
Previamente, la fibra ha sido impregnada por la resina y el conjunto de mateiales utilizados, convenientemente manipulado para que se adopte la forma del molde.
El procedimiento se desarrolla a temperatura ambiente, auqneu puede ser acelerado si aumentamos de forma controlada la temperatura del proceso.
MATERIALES
DESMOLDEANTES
Tienen la función de permitir la separación de la pieza moldeada de la superficie del mode.
Pueden ser de diferente naturaleza:
a.- Vinílicos: Generalmente son disoluciones de alcohol polivinílico, que se aplican mojando la superficie del molde con esponja, o proyectandolos con pistola, produciendo una película que debe secar completamente (15-20 minutos en tiempo seco y temperaturas moderadas)
b.- Ceras Carnauba: Sustancias sólidas que se aplican sobre la superficie del molde, atacando éste progresivamente por zonas reducidas, con la ayuda de trapos limpios y suaves. Para que la cera penetre bien en los poros del molde, su aplicación debe llevarse a cabo efectuando un movimiento circular de la mano y apretando moderadamente. Se recomienda aplicar hasta 5 o 6 veces convenientemente espaciada, sacando brillo en cada operación.
GEL - COATS
Son sistemas a bse de resinas especiales con pigmentos y aditivos en suspensión qeu se emplean para formar lo que serán las superficies exteriores de los plásticos reforzados con fibra de vidrio.
Pueden se aplicados a brocha o a pistola.
Existe una gama muy amplia cuya elección debe efectuarse teniendo en cuenta el tipo de pieza, color deseado, equipo de aplicación, sistema de curado,etc.
RESINA POLIESTER
Son líquidos más o menos viscosos que están formados por la mezcla de:
- Un poliéster no saturado, producto de la condensación lineal de un diácido (maleico, ftálico, etc.), con un dialcohol (glicol, etc.)
- Un monométo no saturado (generalmente estireno)
Estas resinas se conservan en estado líquido durante varios meses, sobre todo en lugares frescos. Para favorecer este estado, el fabricante suele añadir agentes estabilizadores (inhibidores de la polimerización).
Existen diversos tipos de resinas que deben ser selecciondas en función de las exigencias particularesde las piezas a fabricar:
- Rigidas
- Flexibles
- Alimentarias
- Anticorrosivas, etc.
SISTEMA CATALITICO
Para provocar la reacción de polimerización (endurecimietno de la resina), a temperatura ambiente, son necesarios dos tipos de ingredientes:
a.- Acelerado, que activa el catalizador.
Por sí solo no provoca la polimerización y muchos fabricantes suministran la resina ya acelerada. Suele utilizarse el octoato de cobalto en solución al 6%, empleando proporciones comprendidas entre el 0,1 y 0,3% con relación al peso de la resina.
b.- Iniciadores o catalizadores, que tienen la función de iniciar la reacción de polimerización.
Generalmente se utiliza una solución al 60% de peróxido de metiletilcetona en dimetilftalato, en unas proporciones entre 1 y 3% con relación al peso de la resina.
NOTA: Es muy importante tener en cuenta el carácter explosivo de la mezcla catalizador-acelerador, por lo que no deben ser mezclados directamente entre ellos.
REFUERZO
El refuerzo que generalmente se emplea en la estratificación a mano es la fibra de vidrio que se presenta en las siguientes formas:
- Mats de superficie (25-70 g/m2)
- Mats (entre 200 y 900 g/m2)
- Tejidos (300, 500 y 800 g/m2)
De ellos, el Mat es el más empleado en los estratificados normales, aportando la resistencia mecánica el de los gramajes elevados y el mejor acabado superficial con el empleo de Mat de superficie.
con frecuencia se puede hacer una pieza empleando ambos refuerzos, Mat y tejidos.
El espesor y las características de la pieza dependen del refuerzo de vidrio elefido, debiéndose hacer la elección cuidadosamente ya que de ello dependerá el peso y el precio de la pieza.
Elegido el tipo de refuerzo qeuda determinada también la cantidad de resina necesaria teniendo en cuenta que la proporción en peso alzanza el 25-30% de fibra utilizado Mat y el 45-55% utilizando tejido.
METODO OPERATIVO
Asegurese de que la superficie del molde esté prefectamente lisa y seca. En caso necesario aplicar debastadores y pulimentos en función del tipo de material que constituya el molde.
Aplicar el agente desmoldeante, tal y como ya se explicó.
Preparar la resina destinada a la impregnación del refuerzo.
A la cantidad de resina a utilizar se le añade (en el caso de que no se reciba ya acelerada), una cantidad de acelerante a razón del 0,1-0,3% en peso.
Posteriormente se añade catalizador (1-2% en peso). con estos procentajes de catalizador y acelerador, la resina tardará del orden de 30 minutos en gelificar.
Se inicia el moldeo aplicando con pincel una capa de resina sobre el molde.
Sin esperar a que esta resina gelifique se adapta al molde la primera capa de refuerzo. La impregnación de refuerzo se ayuda aplicando más resina sobre el mismo. Se continúa el proceso hasta aplicar el número de capas previsto. Se intentará ir eliminando las burbujas que puedan crearse.
Para desmoldear la pieza debe haber alcanzado la polimerización completa para evitar deformaciones y distorsiones. Para acelerar el endurecimiento, puede introducirse el molde antes del desmoldeo en una estufa de 40-50ºC durante unos 30 minutos.